駕駛室業務的逐步壯大最直接的影響就是型材類零件品種和生產量的增加,與板材相比,型材類零件的生產效率相對較低,再加上品種多,這就對相關零部件的交付提出了考驗。
過程探討
結合我司實際運行方式和現場改善案例,以下將從工藝流程優化、現場定制、MES系統引用幾方面,對提高型材類零件的生產效率的方式進行探討。
工藝流程優化
針對型材類零件,我司主要的零件種類及其對應的生產流程有如下幾種。
⑴直接下料成品,工藝流程為備料成品,如圖1 所示。
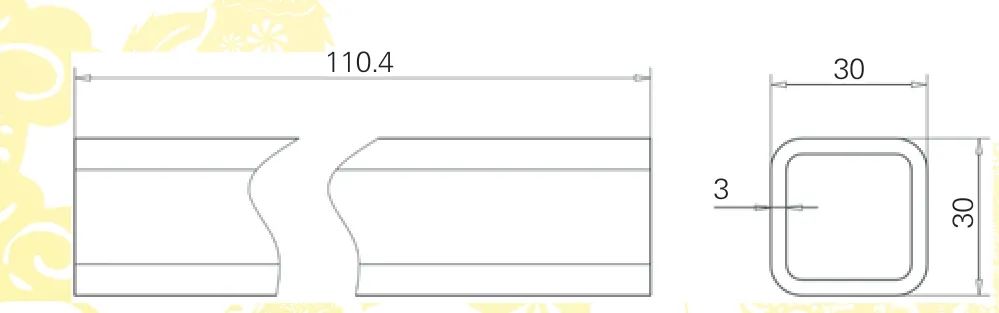
圖1 直接下料成品示意圖
⑵在直接下料成品的基礎上增加孔;即下料后需要鉆孔或者鉆孔攻絲,工藝流程為備料→鉆孔或者備料→鉆孔→攻絲,如圖2 所示。
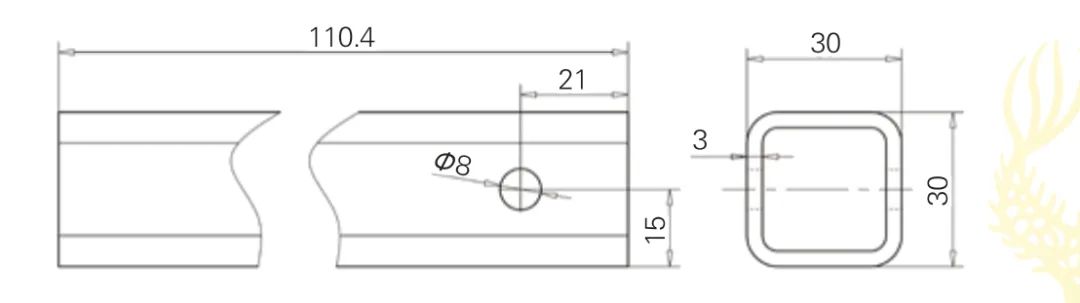
圖2 直接下料后鉆孔產品示意圖
⑶具有一定形狀,無法采用下料的方式進行加工,需要采用模具壓彎或者數控彎管的零件,由于成形過程中需要工藝余料,因此成形后需將該工藝余料去除,其工藝流程為:備料→彎管→鋸切端頭,如圖3 所示。
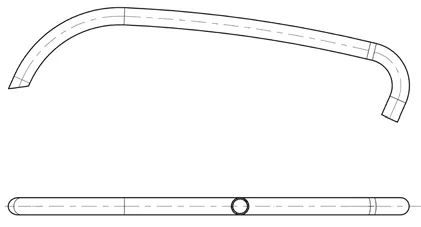
圖3 彎管類產品示意圖
⑷在彎管類產品的基礎上增加規則圓孔,在零件外形加工完成后,需要額外增加鉆孔工序,其工藝流程為:備料→彎管→鋸切端頭→鉆孔,如圖4所示。

圖4 彎管后鉆圓孔類產品示意圖
⑸在彎管類產品的基礎上增加不規則孔,無法使用鉆床進行加工的,需要增加三維激光切割工序,其工藝流程為:備料→彎管→鋸切→三維激光(端頭豁口),如圖5 所示。

圖5 彎管后增加不規則孔類產品示意圖
上述5 種零件是我司目前常見的零件類型,除直接下料成品類型零件外,其余幾種均需要進行轉序,零件轉序就會涉及工序件儲存、轉運,工裝更換,設備更換等因素,這些因素最直接的影響就是零件加工流程延長,從而使成品件的出件時間延長。
針對此類問題,結合我司現有設備能力,利用通快激光設備,對流程進行優化,以減少零件轉序和工序件的產生,具體舉例如下。
針對下料后鉆孔類型零件,直接使用激光進行生產,通快激光作為專業的直管下料類激光設備,具有生產速度快,尺寸穩定性高等特點,適用于生產直管類異型材、型材零件的外形加工。下料后鉆孔類型的零件可以在一序中實現從原材料到成品零件。
針對彎管后加工孔的零件,對零件展開尺寸進行計算,使用通快激光進行下料,之后將下料的半成品進行彎管,實現兩序出成品,大大減少生產過程中的物流轉運和等待時間,以我司生產的某駕駛室用輪罩加強梁為例,零件圖見圖6。
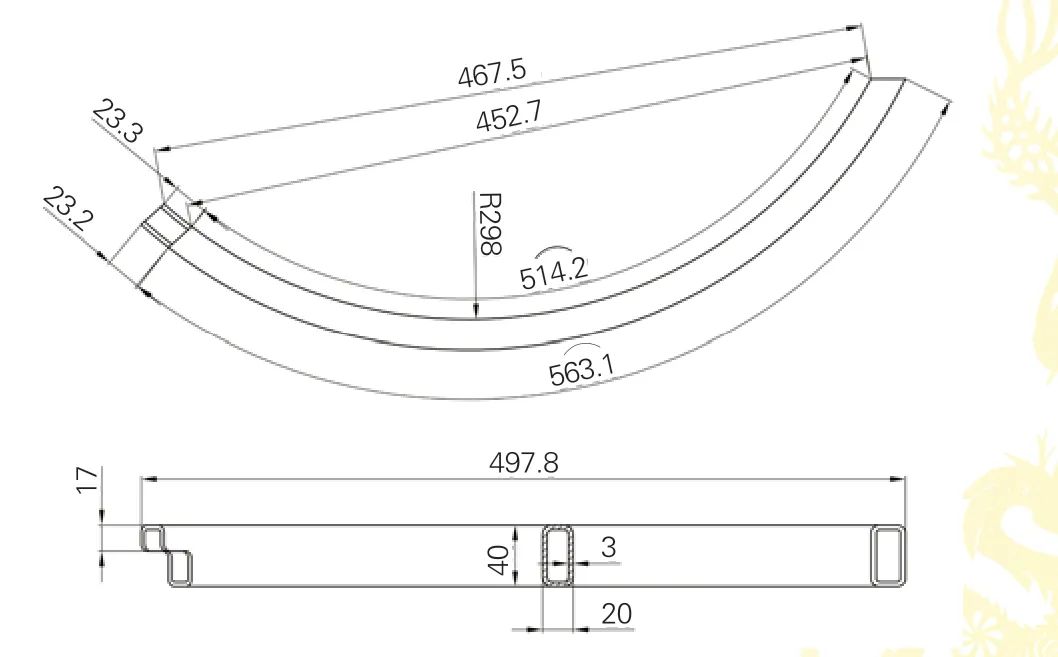
圖6 某駕駛室用輪罩加強梁
優化前工藝流程為:備料→彎管→鋸切→三維激光(端頭豁口)。整個工藝過程需要4 序,流程較為繁瑣,需要更換3 次加工設備,各工序間均可能出現等待的情況,勢必會影響成品件的出件時間。
借助通快加工設備對上述流程進行優化后,流程為:下料→彎管。僅需兩序即可完成零件的加工,具體過程如下。
工序1:下料。將零件展開后所需長度和端頭異形面通過通快設備加工出來,與三維管件激光設備相比,通快激光下料由于是在直管上進行加工,其激光加工效率和基準確定均要大幅快于傳統的三維管件激光設備,如圖7 所示。
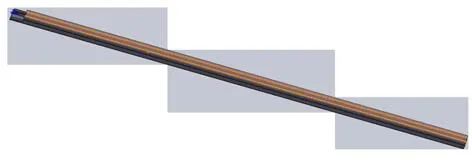
圖7 下料
工序2:彎管。使用數控彎管機對下料后的毛坯進行加工,直接出成品,如圖8 所示。
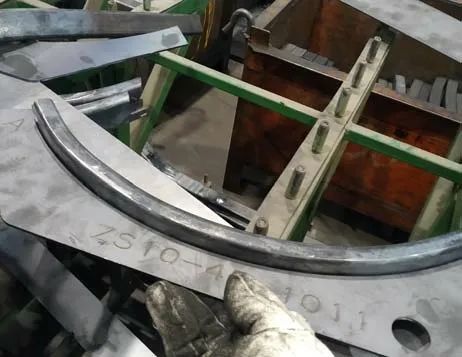
圖8 下料后彎管
從上述可以看出,優化后工藝流程大幅縮短,僅需2 序即可完成零件的加工,說明借助現有資源對工藝流程進行優化,可以對零件的快速實現起到促進作用。
現場定制
在制造類企業中,加工費中的30%左右是搬運費,工程時間中80%是搬運和停滯產生的,因此減少搬運所耗費的時間,將對零件生產效率的提升起到重要作用,而搬運時間的減少就要求科學進行最初的工藝和設備布局,不能一蹴而就。
與板件類零件不同,大多數型材類零件均需要三序或者四序才能實現原材料到成品的轉變,現場定制是否合理,設備與設備之間的配置是否適用,對零件的生產同樣有著直接影響。
借助多年現場經驗,工藝布局和設備定制需遵循以下基本原則:最短距離原則、物流順暢原則、統一原則、安全滿意原則;接下來作逐一說明。
⑴最短距離原則:減少物料在現場的搬運距離,從而減少物料轉移所花費的時間。
⑵物流順暢原則:現場物料或者工序件,實現一個流的生產,避免不同物料或者工序件間的物流交叉,從而減少物料或者工序件的轉運時間。
⑶統一原則:就是“人、機、料、法、環、測”幾大要素要有機統一起來,各個要素之間互相平衡協調,最終實現作業內容的有序進行,沒有割裂。
⑷安全滿意原則:在進行工藝和設備布局時,要以人機工程為基礎,充分考慮作業人員的作業強度和作業步驟是否合理以及作業人員的人身安全。
在滿足上述原則的基礎上,依據實際需求對作業現場進行工藝、設備布局,最終目的是減少搬運和物流轉運時間,在保證作業人員權益的前提下,從硬件層面縮短零件從原材料到成品的時間。

圖9 所示為生產現場布局
MES 系統引用
MES 系統是一套面向制造企業車間執行層的生產信息化管理系統,包含制造數據管理、計劃排程管理、生產調度管理、庫存管理、質量管理、人力資源管理、工作中心/設備管理、工具工裝管理、采購管理、成本管理、項目看板管理、生產過程控制、底層數據集成分析、上層數據集成分解等管理模塊,實現從訂單下達到產品完成的整個生產過程的優化管理。針對我司型材類零件生產,設計用到的MES功能模塊如圖10 所示。
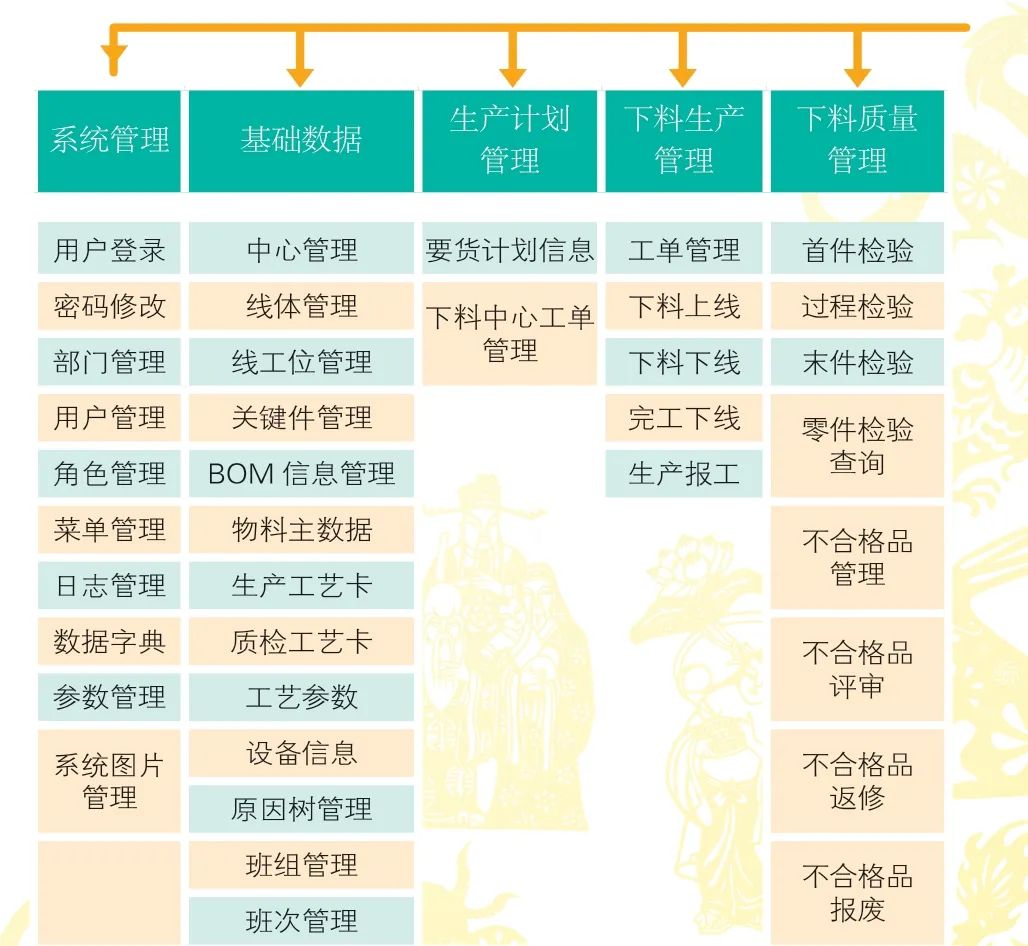
圖10 針對我司型材類零件生產的MES 功能模塊
目前我司已經實現MES 與PLM、ERP系統的對接,可以將ERP、PLM 中的信息在MES 系統中直接調用整合,并且實現了與后序使用單位的MES 接口對接和與后序總成隊列主機號進行綁定。
⑴與后序使用單位接口對接:通過系統操作、在后續總裝隊列基礎上,生產送貨條碼,與總成隊列主機綁定,可以實現物料的一對一,避免出錯,提高交付及時率,如圖11 所示。
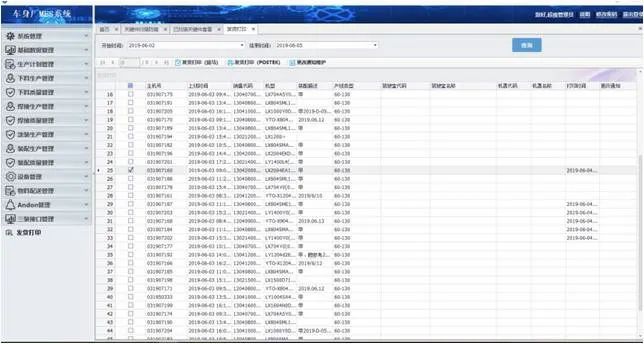
圖11 系統與后序使用單位接口對接
⑵MES 與PLM 系統對接:通過接口實現MES 系統(下料材料投入、下料完工產出)工藝文件在線瀏覽,在PLM 系統通過接口操作,將PLM 系統工藝文件提取、自動上傳至PLM/MES 文件柜下,默認生成的是PDF 文件,文件名為物料編碼,如圖12 所示。
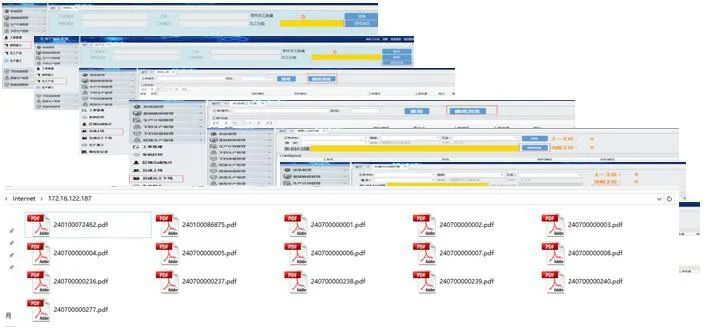
圖12 MES 與PLM 系統對接
⑶MES 與ERP 系統對接:通過實現物料主數據、生產訂單抬頭、組件、工序等接口連接,最終實現物料主數據、BOM 接口、生產訂單接口、AVI 系統接口的統一調配和信息發布,整個生產鏈中管中間、物料數據、BOM 信息、計劃獲取及拆分、相關報表修改、報工等實現自動處理或者少量的人工干預,在大量減少人工操作量的同時,實現制造鏈信息的統一自動調配,對最大化利用現有資源,提高資源利用率有著重要作用。
目前MES 系統正在我司內部逐步深化應用,仍有許多功能模塊正在進行開發調試,但是目前已經實現的模塊已經對我司生產產生了積極影響。
結束語
型材零件由于其本身的特殊性,相對于板件來說,加工效率相對較低,但是通過對流程進行優化、合理的進行生產布局以及引入適宜的管理工具,對型材零件生產效率的提升起到了積極作用。
——摘自《鈑金與制作》 2021年第7期